Stainless Steel Alloy
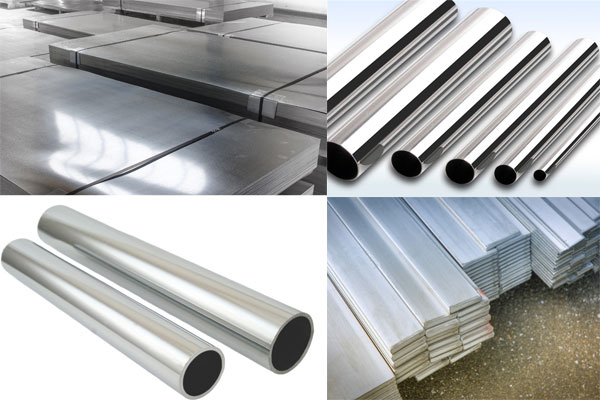
Stainless steels are engineering materials with good corrosion resistance, strength, and fabrication characteristics.
Type 201 is less resistant to corrosion than 300 series. It does have higher yield strength. Some typical end uses include cooking utensils, kitchen equipment, hose clamps, truck trailer structures.
Type 301 has excellent corrosion resistance, high strength and ductility. Typical end uses include auto trim, springs, flatware.
Type 302 resists oxidation, easy fabrication, easy to clean, high strength with low weight. Used for utensils, cookware, and stainless flatware.
Type 302 resists oxidation, easy fabrication, easy to clean, high strength with low weight. Used for utensils, cookware, and stainless flatware.
Type 304, 304L serves a wide range of applications. It withstands ordinary rusting in architecture, it is resistant to food processing environments, it resists organic chemicals, dyestuffs, and a wide variety of inorganic chemicals.
Type 305 low work hardening, high strength to weight ratio, attractive finish, easy to fabricate and clean, excellent for free spinning and cold heading. Typical uses are spring clips, mechanical components.
Type 308 increased oxidation and corrosion resistance over type 305, very ductile, excellent heat resistance, and very good weldability. Some uses include pump parts, oven linings, furnace parts, and boiler baffles.
Type 309 high temperature strength, easy to weld. Typical uses fire box sheets, tube supports, oven linings, and furnace parts.
Type 316, 316L contains slightly more nickel than type 304 giving it better resistance to corrosion than type 304, especially in chloride environments that tend to cause pitting. 316L has superior intergranular corrosion resistance after welding or stress relieving. Easy to maintain, good pitting resistance, superior creep strength, and close tolerances. Typical uses include marine environment components, conveyors, and food processing equipment components.
Type 317 has great resistance to pitting, high tensile strengths. Typically used for storage tanks, chemical processing tanks, and pharmaceutical vessels.
Type 317L excellent corrosion resistance, high creep and tensile strength, high stress to rupture strength, minimizes metallic contamination. Used for storage tanks, and processing tanks for corrosive materials.
Type 321 immune to high temperatures, stabilized by Titanium, resists intergranular corrosion, high strength. Used for aircraft afterburners, exhaust manifolds, cabin heaters, flash boilers, firewalls, and stack liners.
Type 326 great strength, good cold workability, ductile, excellent corrosion resistance. Used for fasteners.
Type 332 resists corrosion, resists oxidation at high temperatures, and superior creep stress rupture properties. Used for boiler and pressure vessels, appliance heating elements, nuclear vessels, and in the food, pulp, petroleum industries.
Type 334 resists scaling, corrosion, and oxidation. Some typical uses, automotive emissions control systems, sheathing for electric heating elements.
Type 347 immune to high temperatures, high strength, stabilized by Columbium and Tantalum. Uses include exhaust manifolds, flash boilers, stack liners, firewalls, pressure vessels and boiler casings.
Type 404 excellent formability, durability, good deep drawing, and good ductility. Common uses include heat exchangers, deep draw parts, automotive components such as radiator and gas caps.
Type 405 easily machined, good ductility, resists oxidation, good corrosion resistance, and easily formed. Typically used for vessel linings, refining equipment, heat exchanger tubing, and quenching racks.
Type 409 has a very low alloy content and is used for highly stressed parts needing the combination of strength and corrosion resistance such as fasteners and automotive exhausts. Other uses include catalytic converters, farm equipment, culverts, transformer cases, and structural supports.
Type 410 corrosion and heat resistant, resists scaling, easily welded, high impact strength, and resists oxidation. Commonly used for turbine blades, cutlery, kitchen utensils, fasteners, screens, bushings, and valve parts.
Type 420 very durable, excellent corrosion resistance, and hardenable to 500 BHN. Typically used for dental instruments, surgical instruments, hospital equipment, gears, molds, dies, knife blades, valve parts, and bushings.
Type 430 has lower alloy content than type 304 and is used for highly polished trim applications in mild atmospheres. Has good formability, ductility, low work hardening, corrosion resistant, oxidation resistant, good thermal conductivity, attractive finish, and excellent for drawing. It is used in nitric acid and food processing. Other common uses include heat exchangers, vaults, tubing, builder's hardware, kitchen trims and appliance trims.
Type 434 easy maintenance, good deep drawing, excellent scaling resistance, good formability, ductility and bright finish. Typical applications include automotive trim, plant machinery, and tubing, refining equipment and chemical vessels.
Type 436 resists scaling, good corrosion resistance, good deep drawing and has bright finish. Commonly used for stretch formed parts.
Type 442 resists scaling, corrosion resistant. Used for furnace parts, stack dampers, heaters, and fittings.