Nimonic alloy Round bar Stockist & Supplier
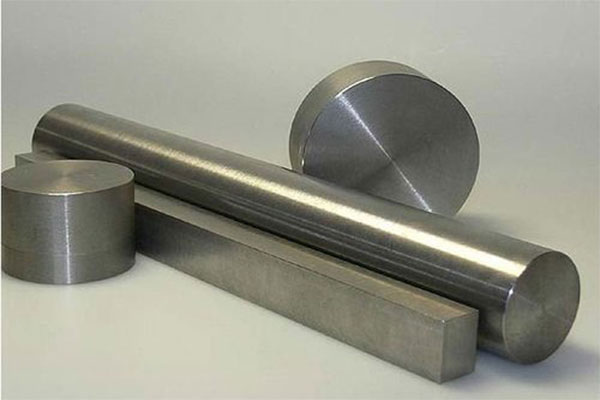
Shree Sambhav Alloys is one of the well known Nimonic Alloy Round bar Stockist. Nimonic is ideally used in the making of aircraft parts and also in gas turbine blades since it is capable of withstanding extreme temperature and pressure conditions. The unmatched quality and unsurpassable performance has attracted various national as well as international clients to place bulk orders for these products. Additionally, customers are facilitated with their availability in varied sizes, dimensions and grades like Nimonic Alloy 80A and Nimonic Alloy 75, as per the specifications and drawings provided.
Nimonic Alloys 80A
Nimonic Alloy 80A (Nimonic® alloy 80A) is a wrought, age-hardenable nickel-chromium alloy similar to NIMONIC alloy 75 but made precipitation hardenable by additions of aluminum and titanium. The alloy has good corrosion and oxidation resistance and high tensile and creep-rupture properties at temperatures to 1500°F (815°C). Used for gas-turbine components (blades, rings, and discs), bolts, tube supports in nuclear steam generators, die-casting inserts and cores, and exhaust valves in internal-combustion engines.
Specifications :- Nickel-Chromium Alloy; UNS N07080; BS 3076 (NA 20), HR1, HR201, HR401, HR601; ASTM B 637; DIN 17742, 17754, Werkstoff Nr. 2.4952, 2.4631; WL Nr. 2.4631, AFNOR NC 20TA; AECMA Pr EN 2188 - 2191, 2396, 2397
Available Product Forms : Sheet, plate, round bar, flat bar, forging stock, hexagon, wire and extruded section
Nimonic Alloys 90
A precipitation-hardenable nickel-chromium-cobalt alloy having high stress-rupture strength and creep resistance at temperatures to about 1700°F (920°C). The alloy also has good resistance to high-temperature corrosion and oxidation. Used for blades and discs in gas turbines, hot-working tools, and springs.
Specifications :-
UNS : N07090
Available Product Forms : Sheet, strip, plate, round bar, flat bar, forging stock, extruded section and wire
Nimonic Alloys 75
Alloy 75 (UNS N06075, Nimonic 75) is a 80/20 nickel-chromium alloy with controlled additions of titanium and carbon. Nimonic 75 has good mechanical properties and oxidation resistance at high temperatures. Alloy 75 is most commonly used for sheet metal fabrications which require oxidation and scaling resistance together with medium strength at high operating temperatures. Alloy 75 (Nimonic 75) is also used in gas turbine engines, for components of industrial furnaces, for heat treating equipment and fixtures, and in nuclear engineering.
Chemical Composition Limits of Nimonic Alloy 80A Round Bars:
Weight % | Ni | Cr | Ti | Al | C | Si | Cu | Fe | Mn | Co | B | Zr | S |
Alloy 80A | Bal | 18.0-21.0 | 1.8-2.7 | 1.0-1.8 | 0.10 max | 1.0 max | 0.2 max | 3.0 max | 1.0 max | 2.0 max | 0.008 max | 0.15 max | 0.015 max |
Chemical Composition Limits of Nimonic Alloy 75 Round Bars:
Weight % | Ni | Cr | Ti | C | Si | Cu | Fe | Mn |
Alloy 75 | Bal | 18.9 - 21.0 | 0.2 / 0.6 | 0.08 / 0.15 | 1.0 max | 0.5 max | 5.0 max | 1.0 max |
Chemical Composition Limits of Nimonic Alloy 90 Round Bars:
Weight % | Ni | Cr | Co | Ti | Al | C | Si | Cu | Fe | Mn | B | S | Zr | Pb |
Alloy 90 | Bal | 18-21 | 15-21 | 2-3 | 1-2 | 0.2 max | 1.0 max | 0.2 max | 1.5 max | 1.0 max | 0.02 max | 0.015 max | 0.15 max | 0.0020 max |
Specifications of Nimonic Alloy Round Bar :
Features : | Cobalt, Strengthened (by heat treatment) with titanium and aluminum additions. |
Applications : | |
Mechanical Data : | MSO currently has no data available for this grade. |
Annealing : | Solution anneal at 1975 F for 8 hours followed by air cooling. |